自電化分公司開展“6S-CTPM”精益管理以來,電儀車間積極響應(yīng)公司號(hào)召,扎實(shí)部署、發(fā)動(dòng)全員、精準(zhǔn)發(fā)力、快速改善、全面推行和實(shí)施6S精益化管理活動(dòng),先后按照公司要求將6S精益化管理納入重點(diǎn)工作,著眼從規(guī)范與效率提升,從工作細(xì)節(jié)入手,對(duì)生產(chǎn)現(xiàn)場、日常工作區(qū)域進(jìn)行全面的整理整頓,并逐一設(shè)置標(biāo)準(zhǔn)化要求,逐步形成了一套行之有效的管理模式,目前電儀車間6S精益管理初顯成效。
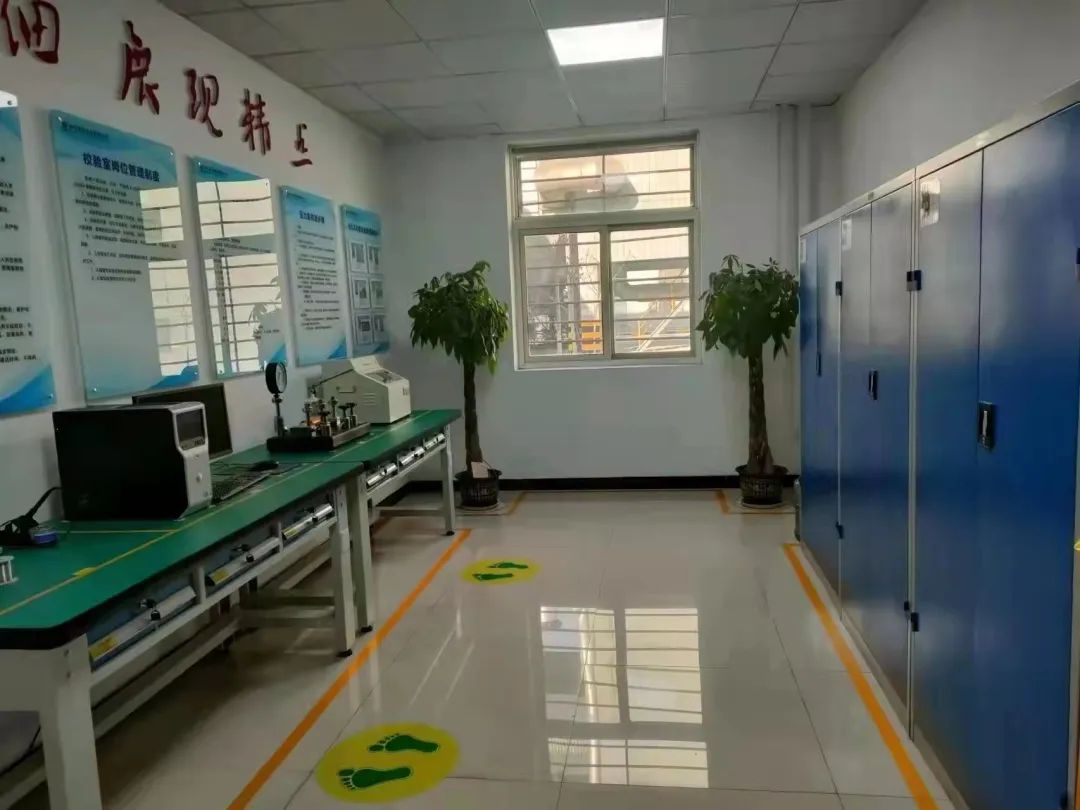
桌面干凈整潔、設(shè)備擺放一條線、各部件標(biāo)識(shí)清楚,柜內(nèi)物品擺放有序、一目了然......這是電儀維修班校室“6S”活動(dòng)打造樣板區(qū)的真實(shí)場景。剛開始的時(shí)候,大家都是盲目的,除了刷著沒完沒了的油漆,就是沒完沒了的定置工具箱、定置桌子、定椅子,很多人都在抱怨,這樣的活動(dòng)還有意義嗎?但當(dāng)那些灰暗的設(shè)備儀器變得色彩斑斕;當(dāng)柜子里那些雜亂無章的材料變得井然有序;原來要花很長時(shí)間才能找到的工具,而如今只要走進(jìn)校驗(yàn)室,所需工具就會(huì)呈現(xiàn)在眼前;當(dāng)雜亂無章的辦公室變得整潔整齊......再也沒有人懷疑6S-CTPM精益化管理活動(dòng)是否有意義,是否值得執(zhí)行了。
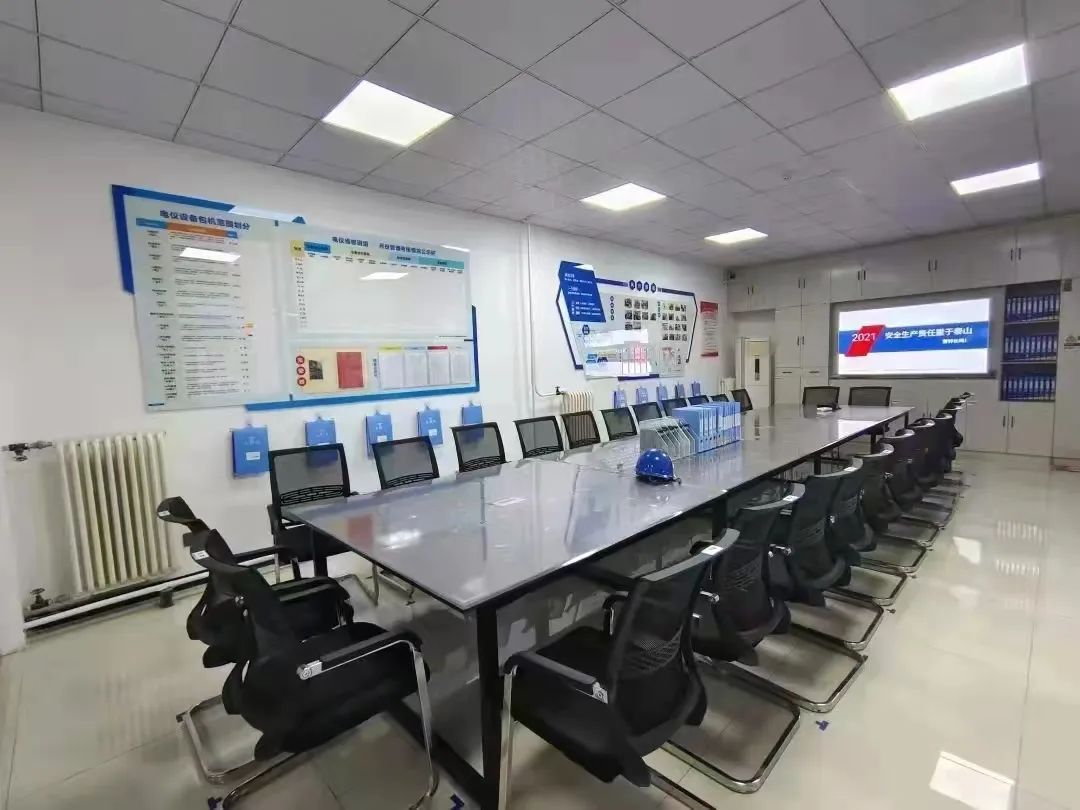
為精益管理活動(dòng)的順利實(shí)施,在車間領(lǐng)導(dǎo)的帶領(lǐng)下,從6S精益管理的制度入手,進(jìn)一步做好全面開展6S精益管理工作,引導(dǎo)員工養(yǎng)成良好的作業(yè)習(xí)慣,提高員工素養(yǎng),定期參加公司組織召開的6S精益管理工作推進(jìn)會(huì),并制定了車間6S 精益管理推進(jìn)計(jì)劃,加強(qiáng)制度建設(shè),把各類制度上墻。持續(xù)完善公司精益化管理的各項(xiàng)制度,推進(jìn)6S精益管理工作向規(guī)范化發(fā)展,通過紅牌作戰(zhàn)計(jì)劃,提升6S精益管理的常態(tài)化,要求全體員工從基礎(chǔ)抓起,從細(xì)節(jié)入手逐步提升精益管理水平,提高員工發(fā)現(xiàn)問題,解決問題的能力。切實(shí)改善了車間的管理面貌,提升了工作效率。通過對(duì)精益管理理念的深入學(xué)習(xí),員工嚴(yán)格按照精益管理標(biāo)準(zhǔn)打造,物有定位、標(biāo)識(shí)清晰、一目了然,既提高了工作效率,又減少了時(shí)間浪費(fèi);修舊利廢多種方式,精打細(xì)算。
車間將”6S-CTPM”活動(dòng)與日常檢維修工作相結(jié)合,持續(xù)開展“OPL點(diǎn)滴教育”活動(dòng),將安全作為不可逾越的紅線,從物的危險(xiǎn)狀態(tài)、人的不安全行為和管理缺陷等方面著手,對(duì)車間辦公區(qū)域、所管轄設(shè)備設(shè)施、班組記錄等進(jìn)行清掃和整理,并且利用工作時(shí)間之余加大對(duì)員工的技術(shù)培訓(xùn),有效地提高了員工業(yè)務(wù)能力素養(yǎng)和設(shè)備維護(hù)率。增加了設(shè)備使用壽命和安全運(yùn)行指數(shù),在對(duì)爐變油冷器設(shè)備初期清掃中,員工能夠積極發(fā)現(xiàn)問題,進(jìn)行原因分析,最后做出合理整改,在整改過程中,員工以安全為中心,對(duì)設(shè)備故障進(jìn)行整改,確保設(shè)備以最佳狀態(tài)運(yùn)行。同時(shí),車間不斷強(qiáng)化員工精益管理意識(shí),結(jié)合生產(chǎn)實(shí)際,把精益管理理念落實(shí)到實(shí)際工作當(dāng)中,通過加強(qiáng)備品備件方面的管理,強(qiáng)化設(shè)備點(diǎn)檢,杜絕“跑、冒、滴、漏”現(xiàn)象。
一分耕耘,一份收獲?!?S-CTPM”精益管理是一個(gè)只有起點(diǎn)沒有終點(diǎn)的持續(xù)改進(jìn)的過程,需要不斷地探索、實(shí)踐。6S精益管理永遠(yuǎn)在路上。接下來,電儀車間將在做好整理、整頓、清掃、清潔的基礎(chǔ)上,繼續(xù)培養(yǎng)員工良好的行為習(xí)慣,建立健全管理的長效機(jī)制,保持常態(tài)化、規(guī)范化、制度化,朝著標(biāo)準(zhǔn)化和精細(xì)化管理不斷邁進(jìn)。(王亞麗)